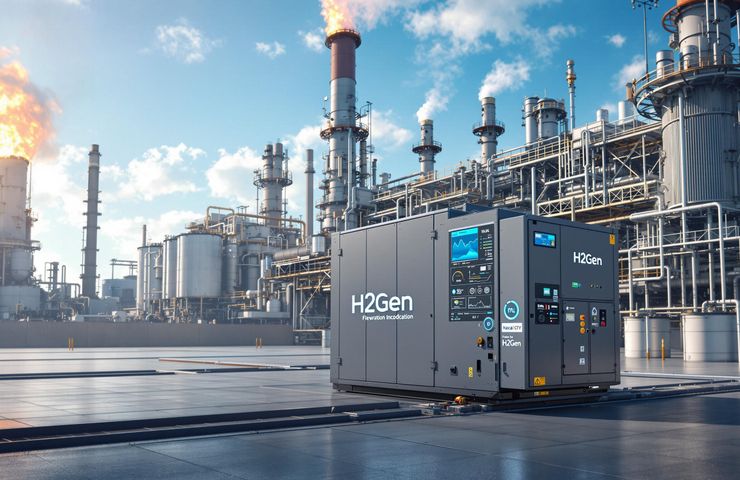
Hydrogen Production Just Got a Major Upgrade — Without the Electricity
July 11, 2025Utility Global and Rockwell Automation have pulled off something pretty remarkable—they’ve managed to produce hydrogen on a commercial scale using blast furnace gas (BFG) from a steel plant, and get this: there’s no electricity involved in the actual hydrogen-making step. That’s a first. This game-changing breakthrough has already racked up over 3,000 hours of real-world operation at a steel facility in North America.
Reimagining waste as a clean hydrogen source
At the heart of it all is Utility Global’s H2Gen platform. Instead of letting industrial off-gases go to waste, it repurposes them—along with water—to generate clean hydrogen. The process doesn’t just stop there. It also captures a concentrated stream of CO₂ as a byproduct, making it easier to manage emissions downstream.
Smart tech meets clean energy
To make sure everything runs like clockwork and can scale up smoothly, Rockwell Automation brought in its PlantPAx control system. It’s the backbone that keeps the entire operation stable and future-ready, proving that high-performance automation has a big role to play in today’s clean energy economy.
Paving the way for industrial decarbonization
Why does all this matter? Because traditional hydrogen production methods—especially using electrolyzers—are expensive and demand a lot of infrastructure. This new approach flips the script. By turning waste gases into a valuable resource, heavy industries like steelmaking now have a real shot at cutting emissions without overhauling their entire operations.
This kind of innovation is what the future of industrial decarbonization looks like. It shows that hydrogen production can be cleaner, more efficient, and better integrated into existing industrial systems. And it’s a big leap forward as green hydrogen and reliable hydrogen infrastructure become central to transforming hard-to-decarbonize sectors.