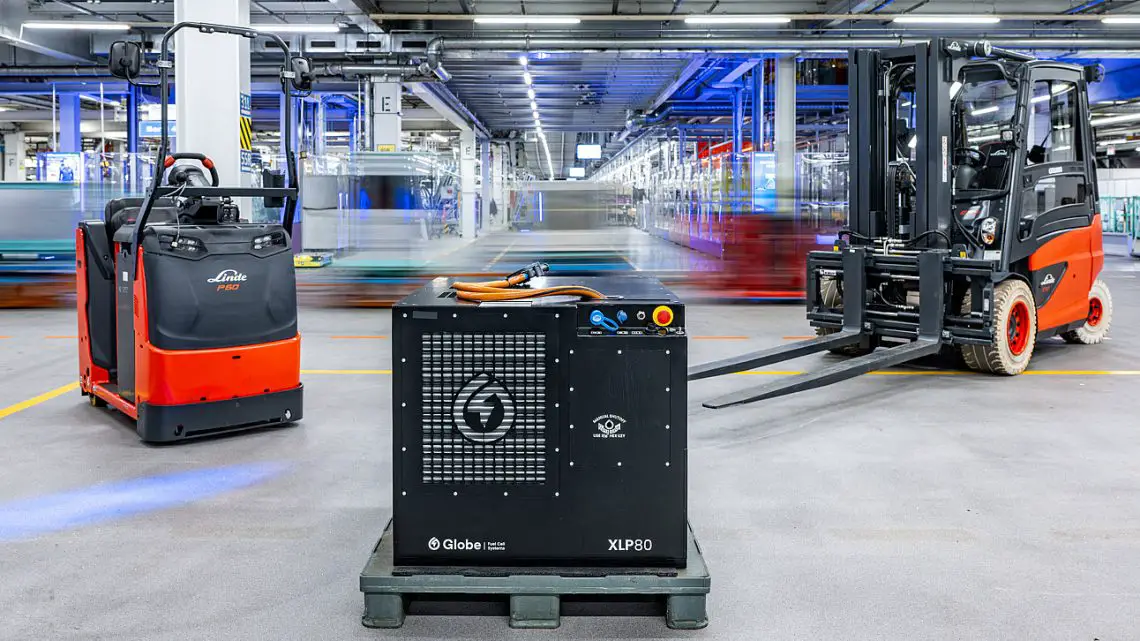
BMW Group Plant Regensburg Drives Toward Hydrogen-Powered Logistics by 2030
November 26, 2024BMW Group Plant Regensburg Drives Toward Hydrogen-Powered Logistics by 2030
The BMW Group Plant Regensburg is forging ahead with an ambitious plan to revolutionize its logistics processes by integrating hydrogen propulsion systems. This transformation is set to begin in 2026, with the introduction of hydrogen-powered tugger trains and forklift trucks, aiming for a full transition from electric to hydrogen propulsion by 2030. The initiative aligns with BMW’s broader vision for sustainable and digitized manufacturing under the BMW iFACTORY framework.
Hydrogen in Production Logistics
The push for hydrogen-powered logistics at Plant Regensburg targets areas where efficiency, sustainability, and space constraints converge. Starting with operations in critical zones such as the press shop, body shop, and assembly areas, hydrogen-powered vehicles will be tasked with ensuring that components and parts are delivered to the right production points seamlessly.
Currently, the factory’s logistics fleet is predominantly electric, with batteries requiring manual changes twice per shift—a process that consumes both time and space. Hydrogen propulsion offers an efficient alternative. “The advantage of hydrogen is that refuelling is very fast – just like with conventional fuels,” explains Katharina Radtke, Project Manager at BMW Group Plant Regensburg. Custom-built hydrogen filling stations, compact in design, will be installed within production zones to further streamline operations.
Armin Ebner, head of BMW Group Plant Regensburg, underscores the larger vision behind the transition. “The gradual transition from electric to hydrogen propulsion brings us another step closer to the BMW iFACTORY, our digital and sustainable factory of the future,” he states. The shift not only optimizes logistics processes but also diversifies the energy infrastructure within the plant.
Building Hydrogen Infrastructure
To facilitate the adoption of hydrogen, BMW Plant Regensburg is laying the groundwork for a robust supply network. A two-kilometre-long pipeline system, supplemented by six decentralized filling stations, is set to be operational by early 2026. Special hydrogen trailers will transport and store the fuel efficiently. Once fully implemented, BMW Plant Regensburg’s logistics operations are projected to consume around 150 tonnes of hydrogen annually.
The current logistics fleet comprises approximately 230 tugger train haulers and forklift trucks. By adopting hydrogen propulsion in stages, the plant aims to ensure the continuity of operations while gradually reducing its reliance on electric drive trains.
Advancements and Partnerships in Hydrogen Technology
BMW isn’t pursuing ventures in hydrogen in isolation. Their efforts signal broader advancements and collaborations in hydrogen propulsion technology:
-
Advanced Hydrogen Drive Trains
BMW has developed hydrogen powertrains that combine fuel cells with advanced lithium-ion batteries, providing greater energy density and performance optimization. -
Collaborations for Fuel Cell Development
Partnerships with companies such as Toyota have enabled BMW to co-develop next-generation fuel cell systems, offering reliable, high-capacity energy solutions tailored to large-scale industrial and automotive use. -
Hydrogen Station Rollouts
Collaborations beyond the automotive scope include infrastructure projects with energy specialists to expand hydrogen refuelling networks at both public and industrial levels. -
Zero-Emission Solutions
Hydrogen technology has been integrated into BMW’s research for emission-free mobility alternatives, supporting a future framework that bridges passenger vehicles and logistics systems.
These initiatives contribute to refining hydrogen propulsion, ensuring compatibility with heavy-duty tasks while establishing scalable infrastructures.
Scaling Potential Beyond BMW
While the introduction of hydrogen logistics aligns with BMW’s sustainability goals, the potential impact of this shift is not limited to the automotive industry. Overcoming the hurdles of electric vehicle limitations—such as frequent battery changes and downtime for charging—hydrogen-powered logistics offer a compelling solution in industries reliant on large-scale goods movement.
Fast refuelling times, compact station designs, and flexibility in hydrogen distribution mean that this technology can improve operational workflows across warehousing, manufacturing, and even agriculture. For example, logistical hubs can deploy hydrogen vehicles to enhance productivity by minimizing energy-related delays. Additionally, industries with decentralized production sites could integrate hydrogen pipelines to power a consistent energy supply, eliminating bottlenecks related to existing systems.
Projections suggest that as hydrogen infrastructure grows, costs associated with its production, storage, and distribution will reduce over the next decade. This trajectory creates opportunities to adopt hydrogen technology more affordably and with greater efficiency, particularly in sectors where other renewable energy solutions may fall short.
Looking Ahead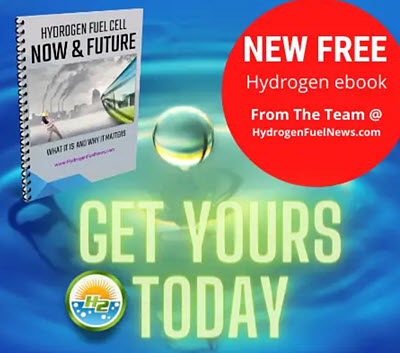
The planned transition at BMW Group Plant Regensburg illustrates a forward-thinking adaptation to current logistical challenges. Hydrogen-powered systems offer clear benefits—reducing downtime, maximizing operational space, and creating cleaner energy solutions. These advantages translate well to industries striving for similar efficiencies while mitigating environmental impacts.
Scaling the hydrogen ecosystem will require collaboration between industries, energy providers, and governments to establish cost-effective supply chains and affordable fuel cell technologies. Today, smaller-scale trial implementations, such as those seen in BMW’s logistics fleet, demonstrate an achievable pathway to reduced emissions and improved logistics operations. With these practical applications already taking shape, the long-term potential of hydrogen propulsion appears both promising and actionable.