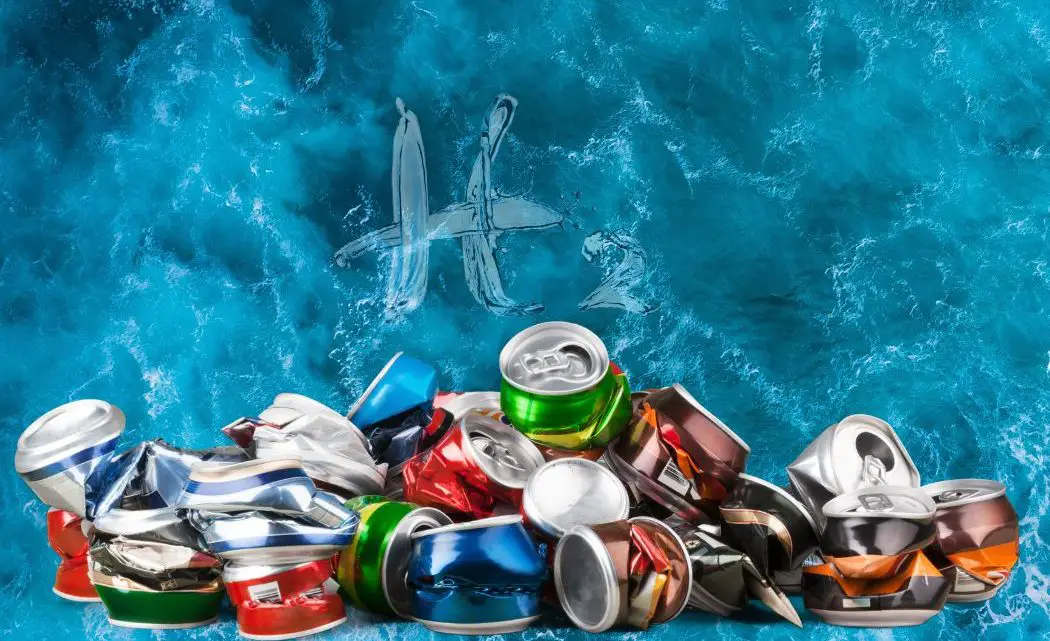
Generating Hydrogen from Seawater Using Soda Can Aluminum
July 30, 2024A groundbreaking discovery has revealed that aluminum from soda cans, when purified and mixed with seawater, can generate hydrogen gas, a clean energy source for engines and fuel cells without carbon emissions. This innovative process is enhanced by the addition of imidazole, a compound found in caffeine from coffee grounds.
During experiments, pretreated aluminum pellets were introduced into filtered seawater, resulting in the production of hydrogen gas. The pretreatment involves a gallium-indium alloy, which removes the oxide layer that usually inhibits aluminum’s reaction with water. This technique ensures a pure form of aluminum that reacts efficiently with seawater to produce hydrogen. Notably, the gallium-indium alloy can be recovered and reused, making the entire process sustainable.
Research and Development at MIT’s Department of Mechanical Engineering
MIT’s Department of Mechanical Engineering spearheaded the development of this groundbreaking hydrogen production process. Led by Kombargi, the team conducted experiments to optimize the system’s efficiency, exploring various configurations and conditions.
A significant part of their research involved using seawater from Revere Beach to test the reactor in real-world conditions. This approach validated their theoretical model and highlighted the technology’s practical applicability in utilizing coastal resources. Their successful tests indicate the potential for large-scale implementation, positioning this innovation as a leader in sustainable energy solutions.
Milestones and Future Endeavours
This study was published in the journal Cell Reports Physical Science, marking a significant milestone in the research team’s journey. The publication serves to highlight not only the innovative process of hydrogen production but also the potential impact on the clean energy sector. The team at MIT, led by Kombargi and Tsakiris, is actively refining their system to enhance efficiency and reliability. In upcoming experiments, they plan to test the hydrogen generation technology in practical applications, including marine vessels and underwater vehicles.
This forward-thinking approach aims to assess real-world performance and gather valuable data that could inform future advancements. Their vision extends to scaling up the production process, paving the way for larger applications that could significantly contribute to a sustainable energy ecosystem, ultimately reducing dependence on fossil fuels and facilitating a transition to greener energy alternatives.
The need for clean, sustainable energy sources has become increasingly urgent in recent years. Fossil fuels are not only finite, but also contribute significantly to pollution and climate change. The team at MIT recognized this pressing issue and set out to find a solution that could potentially revolutionize the clean energy industry.
How the Green Hydrogen Production Process Achieves Efficiency and Simplicity
The process of producing hydrogen fuel using aluminum pellets and seawater is relatively simple yet highly efficient. The aluminum pellets, once pretreated with gallium-indium alloy, react with water to produce hydrogen gas through a chemical reaction known as hydrolysis. This gas can then be collected, stored, and used as a clean energy source.
A small, pebble-sized pellet of aluminum, when introduced into a beaker of filtered seawater, rapidly initiates a chemical reaction that produces hydrogen gas, which swiftly bubbles to the surface within minutes. MIT engineers are diligently refining this straightforward yet effective reaction to create a sustainable method for generating hydrogen fuel.
Steps: Hydrogen from Seawater Process, a Simplified Explanation:
- Pre-treatment:
- Aluminum pellets are treated with a gallium-indium alloy to remove any oxide layers, exposing pure aluminum.
- Hydrogen Production:
- The treated aluminum pellets are placed into filtered seawater, initiating a reaction that produces hydrogen gas and heat.
- Adding imidazole, an active ingredient in caffeine, significantly speeds up the reaction, reducing the hydrogen production time from two hours to just five minutes.
- Sustainability:
- The gallium-indium alloy is recovered from the seawater using an ionic solution, allowing it to be reused for further pre-treatment of aluminum pellets.
Detailed Breakdown of Chemical Reactions:
- Pretreatment of Aluminum Pellets:
- Gallium-indium alloy removes the passivating oxide layer from the aluminum, exposing pure aluminum.
- Main Reaction with Seawater:
- The exposed aluminum reacts with water in the seawater to produce aluminum hydroxide and hydrogen gas.
- Aluminum hydroxide further reacts with water to form aluminum oxide and additional hydrogen gas.
- Role of Caffeine (Imidazole):
- Imidazole pierces through the reformed oxide layer on the aluminum, maintaining continuous reaction with water.
- It protects the gallium-indium alloy, ensuring its reuse.
- Recovery of Gallium-Indium Alloy:
- Ions in seawater help recover and recycle the gallium-indium alloy for further use.
- Overall Reaction Equations:
- 2Al + 6H2O → 2Al(OH)3 + 3H2
- 2Al(OH)3 → Al2O3 + 3H2O
Future Prospects
The next step for the MIT team involves testing the hydrogen reactor on marine vessels and underwater vehicles. Calculations suggest that a reactor holding about 40 pounds of aluminum pellets could power a small underwater glider for approximately 30 days. The team envisions this technology being extended to trucks, trains, and possibly airplanes in the future, with the potential to extract water from ambient humidity to produce hydrogen.
very interesting research, At now, I´m developing a research that aims to identify the ideal parameter for sustainable hydrogen production with zero or negligible level of risk of an interesting alternative that can be obtain H2 through the chemical reaction between aluminum and water catalyzed by an alkaline solution. Although hydrogen is an important form of energy, its production involves peculiar aspects. For the proposed study, the great advantage of generating hydrogen in a simple way, with very low electricity consumption and low cost it is associated with some relevant aspects. The chemical reaction is strongly exothermic, the gas produced is flammable, asphyxiating, has high calorific value and the chemical agents and residues involved present causticity and considerable toxicity. This represents risks to the people, to the environmental conditions and also to fire. Thus, in order to this project to receive definitive approval from government authorities for environmental inspection, occupational health and safety and the Fire Department, a complementary Risk Management Project (RMP) becomes decisive. In order to offer an effective study, a methodology was identified that has innovative characteristics, such as a new conceptualization of risk, unmistakable technical conducts for the unequivocal identification of all associated risks and the best practices of conducts to neutralize or eliminate and control the related risks and others very interesting ones. The research will be developed through zero-order mathematical simulations to determine optimal design and operating parameters with zero risk or at least at an acceptable level. The study will start from the initial condition, when the yield of the gas production will be evaluated. At the same time, a RMP will be developed to manage the risks. Once defined, the risk control actions will be implemented in the system and another round of tests will be carried out and the new results can be compared with the initial condition. Identifying differences, adjustments both in the operating conditions of the system and in the RMP guidelines should be made and new and subsequent tests should be carried out until the ideal condition for hydrogen production with minimum acceptable risk is obtained. Then, in an innovative way, a project for the technical development of a device of relevance to the community that will generate sustainable hydrogen will be offered properly optimized and under strict and effective risk management conditions to offer absolute safety to users, to the environment and to facilities with a focus on fires.