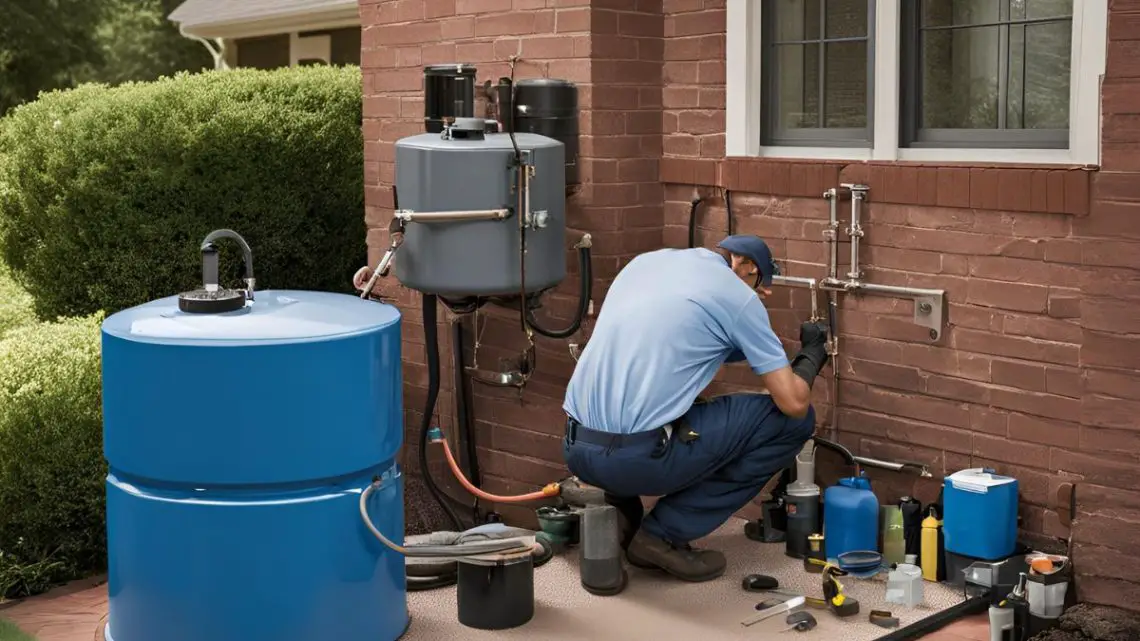
A Comprehensive Guide to Oil Tank Maintenance and Safety
December 19, 2024Amazing development marks our path towards better methods of storing oil. Fresh data shows 2022 as a turning point – achieving unheard-of safety records in offshore oil and gas activities. This success point emphasizes a more general change occurring in tank maintenance procedures in all kinds of industry.
The point of oil tank replacement has far more weight than it did years ago. Residential tanks usually serve dutifully for 15 to 20 years with adequate maintenance; but industrial facilities have growing maintenance needs. These difficulties also affect home configurations and large-scale industrial complexes where one error could cause disastrous results.
Out of 77 reportable events last year, hydrocarbon leaks dominated harmful events accounting for 52 of them. Such numbers immediately highlight why proactive maintenance is so important. Environmental stakes also loom especially big: leaking oil could contaminate rivers, endanger species, and cause expensive clean-ups.
Still, these difficulties present opportunity, as with most things. Modern monitoring systems, improved safety precautions and more intelligent maintenance plans help guard our environment and assets. Understanding correct tank maintenance helps us to protect our equipment, our communities, and the natural environment.
Key inspection procedures
Of tank mishaps, fire and explosion account for 85%. Your weekly visual checks consequently act as a front line protection against possible disasters. Look for clear indicators of problems: rust spots, dents or distortions near joints and seams. Focus especially on places where moisture usually gathers. Often, these brief but thorough inspections find early warning indicators before issues get worse.
More solid insight into tank condition comes from annual professional inspections. Certified professionals use specific tools to evaluate structural integrity and find patterns of hidden corrosion. They examine supporting systems, looking for foundation flaws or settlement problems that might jeopardize tank stability.
Monitoring contamination is similarly important. Particularly affecting tank lifetime and compromising gasoline quality is water intrusion. Modern ultrasonic testing finds interior corrosion sites not seen with human vision. When issues develop, smart sensors track moisture levels and send real-time alarms.
Remember too that leak detection calls for particular attention. Extensively check all pipe connections valves and gaskets. Look for unusual environmental changes close to tank sites or gasoline loss. Unchecked, small leaks eventually become huge concerns.
By means of constant application of these inspection techniques, we significantly lower accident risks. See every inspection as an investment in safety instead of as a legal need. After all, preserving life property and environment begins with constant monitoring of our storage facilities.
Mastering regular maintenance
Every tank owner should pay close attention since diligent maintenance greatly increases tank lifespans of up to 20 years. This lifetime results from applying thorough care plans instead of sporadic visits.
Naturally, professional cleaning is part of this. Plan comprehensive cleanings based on environmental conditions and usage patterns every three to five years. These deep-clean sessions eliminate accumulated sludge sediment and water, well known causes of interior corrosion. Your cleaning calendar might have to change depending on local temperature conditions or fuel flow.
You also have to think about the battle against corrosion process too. Start with professionally applied premium protective coatings covering internal and outdoor surfaces. Modern epoxy-based treatments provide better protection than more conventional approaches. While well positioned water traps capture condensation before causing damage, moisture barriers around tank bases prevent ground dampness from increasing degradation.
Think about getting smart tech too, since automatic gauges offer real-time information on fuel level integrity and possible issues. From slight pressure fluctuations to major leaks, these systems notify you when they find anomalies.
Although sometimes disregarded, filter maintenance is rather important. Depending on manufacturer recommendations and usage patterns, replace filters often. Filtered systems that are clogged strain pumping systems maybe causing fuel contamination or component failure. Carefully scheduled replacement dates provide best system performance.
Mastery of maintenance calls for more than just following guidelines. Knowing how various parts interact helps one predict possible problems before they become more serious. Your proactive maintenance not only guarantees safe dependability for the whole running life of your tank but also safeguards your investment.
Risk control and emergency procedures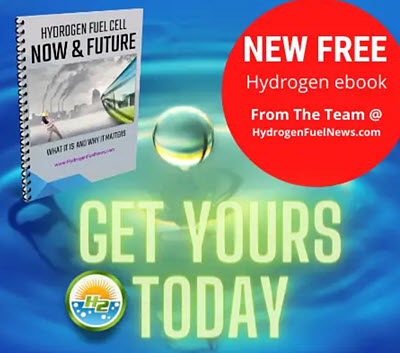
With 52 out of 77 recorded events, hydrocarbon emissions dominated harmful events last year. These figures show why strong risk control and emergency procedures are still very vital for tank operators.
Knowing shut-off valve locations marks the beginning of your emergency readiness. Clearly highlight these important locations indicating main and secondary shutdown choices. Smart operators keep current facility schematics including emergency equipment locations and regions of containment and drainage routes.
Constant practice and updates are absolutely necessary for emergency response protocols. Staff members should be well trained on shutdown processes, spill control techniques, and evacuation policies. Keep emergency contact numbers close at hand; including local officials from environmental agencies, cleanup experts.
By using professional associations and regulatory updates, you can keep current with evolving rules. Carefully record all maintenance activity and incident reactions; during audits, this material is quite helpful as it enables historical tracking of system performance.