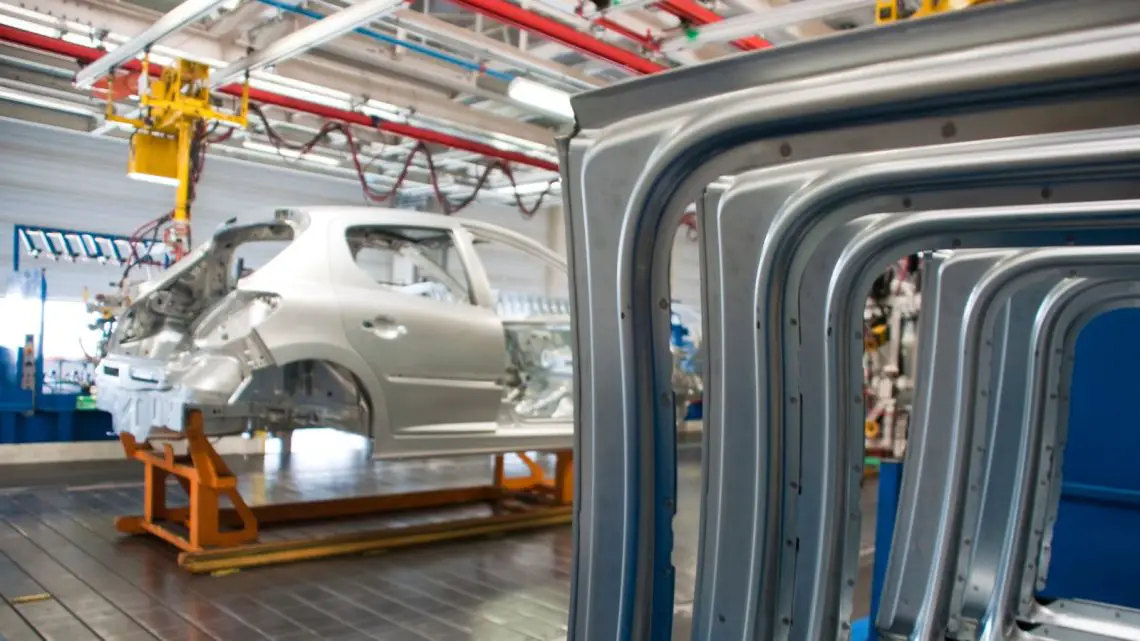
The Application of Machining Parts in New Energy Vehicles
February 28, 2023The new energy vehicle industry has become one of the largest and most important industries in the last decade, and innovation is a key part to make these new technologies affordable and efficient. In this sense, the manufacturing processes require tighter tolerances and CNC services, require advanced grinding, milling, and drilling machines and combined technologies are needed to satisfy the high demand for new energy vehicles.
CNC machining prototyping and general machining processes bringing to the development of new energy vehicle manufacturers. Hence, new tools and technologies should be implemented to allow the new energy vehicle manufacturers to stay competitive in the automotive industry.
Body and Chassis
Panels placed in body parts are manufactured with special molds and dies, machined with powerful machining centers with multiple axes (4 and 5). Car structure requires lightweight materials that are hard to machine with conventional processes. Hence, manufacturers rely on CAD/CAM softwares to simulate the cutting of these new materials and, to see in advance the possible outcome of the molded parts.
Also, advanced CNC routers and milling machines are used to manufacture interior parts of the car. Those include panels, gauges, and light cases. These are often made of acrylic and thermoresistant polymers, needing precise lasers with higher speeds and quality cutting such as hybrid fiber lasers like the new S-MOPA laser (Solid-State Master Oscillator Power Amplifier).
Braking System
Braking systems in new energy vehicles are very similar to traditional vehicles, including bearings, braking discs, pads, studs, and plates, often produced at scale using CNC services (using milling machines and lathes). Especially those parts with tighter tolerances such as bearings, joints and ratchets.
Both braking and body parts of new energy vehicles tend to be made of lightweight materials to reduce driving noises and facilitate machinability in soft metal alloys. New CNC technologies are improving surface finish in the materials that were previously classified as difficult-to-machine materials.
Motor and Its Components
Rotary shafts, linear ball bushings, and configurable plates can only be made with precise and modern milling and drilling machines, often aided by co-bots (vision system robots) for automation purposes. According to the specialists, co-bots are set to become technicians’ coworkers soon, to increase productivity and reduce human errors.
Due to the demand for perfect surface finishing and precise manufacturing, CAM/CAD software companies have developed new software packages and controllers such as Mastercam Multiaxis, which automatically produces tool paths for making automotive dies and for cutting intricate parts with deep holes and pockets in the most effective way.
This software allows the simulation of every stage of machining and highlights possible mistakes, collisions and deviations. More details of this software tool are found on their official website.
Plus, collision risks led manufacturers to incorporate vacuum fixtures and modern vacuum tables to improve part holding and provide a secure adjustment to CNC machines. Especially when working with big plates, a very common situation in the automotive industry.
Battery
High-resistance battery trays and battery support, demand complex designs and the use of thermal-resistant materials. These trays are usually made of aluminum, which increases friction in the milling processes and involves high amounts of cutting lubricant. Also, battery trays need precise cutting tools to drill and tap intricate holes and pockets.
Battery packs in electric vehicles need to be more secure compared to their ICE counterparts since electric motors operate at higher speeds and generate more friction.
Researchers are now focusing on replacing lead acid batteries with silicon and gel batteries without altering the costs of vehicles.
Driving system
New energy vehicle manufacturers are focusing on incorporating self-driving systems to compete with traditional vehicles while incorporating Artificial Intelligence in every step of the process. Not only for driving software and vehicle electronics but also at manufacturing stages where new CNC machines use AI to self-diagnose, improve productivity, and reduce downtime errors.
Self-driving technology is the present and future of the automotive industry and is intended to sense the vehicle’s environment without human input or minimal interaction. This requires that mechanical and electrical parts are flawlessly made, demanding high-quality and precise CNC services.
Challenges of Machining Parts in New Energy Vehicles
- High Cost
New energy vehicle manufacturing involves the cost of new technology development. a lot of research and material experimentation, competitive charging systems like high-performance lithium or cobalt batteries, charging stations, and infrastructure, even the raw material used in batteries’ manufacturing increases exponentially the overall price of the vehicles.
Also, since the new energy vehicle is still a growing industry, there are fewer market competitors, immediately causing high prices since demand exceeds supply. In addition to that, new energy vehicles are often associated with luxury brands such as Tesla Motors and its EVs. This consumer behavior continues to position NEVs as one of the most expensive automobiles in the market.
- Complexity of Design
Since NEVs are not designed around an internal combustion engine, engineers need to optimize the design space and rely on simulations to evaluate prototypes. That’s where the CNC machining prototyping becomes more relevant than ever. Engineers also face intricate geometry configurations in terms of the battery pack and battery cells and how to enhance their performance to compete with gas-powered vehicles.
Also, the fact that electric motors produce less noise and vibrations has created new challenges for more aerodynamic designs to cover conventional noises that become more prominent in these vehicles such as wind, chassis, and brake noises.
- Limited Availability of Parts
New energy vehicles are far more reliant on semiconductor chips than traditional vehicles, which can cause performance failure in NEVs systems. These components are manufactured by external suppliers delaying replacement efforts. A similar scenario occurs with battery manufacturers from different brands and models. However, the aftermarket and repair industry for new energy vehicles is still growing and although finding spare parts can be time-consuming, new-energy vehicles are known to be a low-maintenance alternative for drivers.