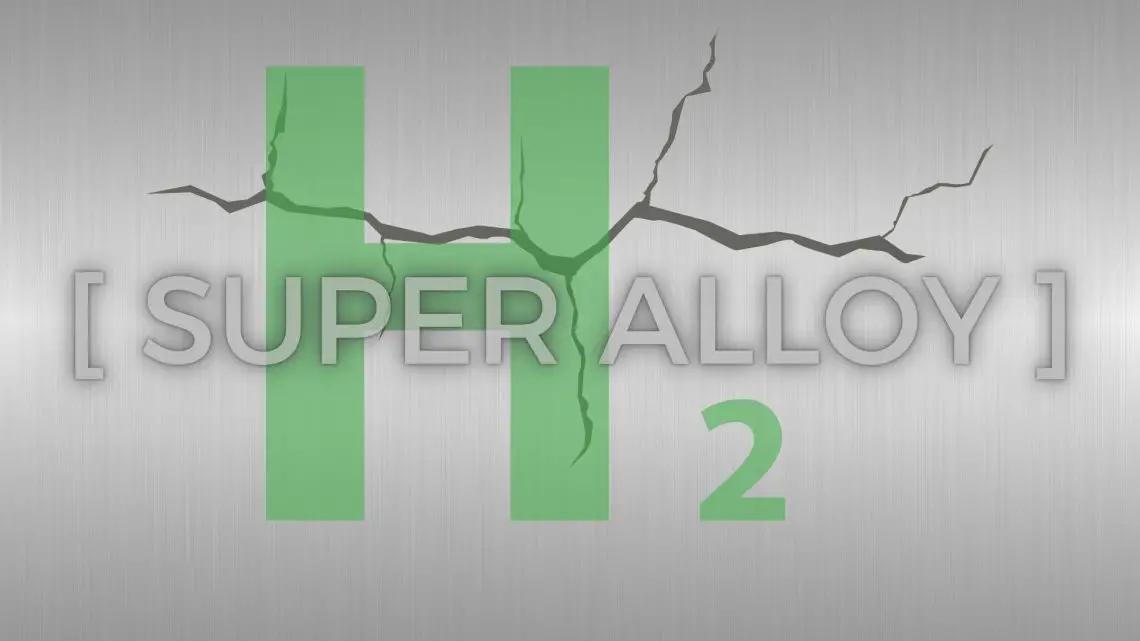
Finding A Weakness in Superalloy can turn into innovation
November 5, 2024Unveiling the Science: Hydrogen Embrittlement in Inconel 718
Recent scientific advancements have shed light on a critical challenge for Inconel 718—hydrogen embrittlement, a phenomenon where hydrogen exposure weakens the metal, leading to brittleness and cracking. This discovery is pivotal, especially as hydrogen gains traction as a sustainable energy source.
Researchers have delved into the interactions between hydrogen and Inconel 718, paying special attention to the differences between its *additively manufactured (AM) and traditional wrought forms. Their findings reveal that microstructural variations significantly influence hydrogen absorption and susceptibility to embrittlement.
In AM Inconel 718, dislocation cells—tiny, densely packed regions—act as traps for hydrogen, making it more prone to embrittlement than its wrought counterpart. Armed with this knowledge of the alloy’s weaknesses, scientists are now actively working on strategies to mitigate these vulnerabilities and enhance its resilience.
The Go-To Material: Unmatched Properties Powering Diverse Industries
- High Temperature Resistance: Maintains strength and stability at elevated temperatures.
- Corrosion Resistance: Withstands harsh environments, including oxidizing and corrosive conditions.
- Versatility: Suitable for complex shapes and applications due to its robust mechanical properties.
Applications of Inconel 718:
- Aerospace: Used in jet engines and other high-performance aerospace components.
- Energy: Essential in gas turbines and nuclear reactor components.
- Oil and Gas: Utilized in drilling equipment and offshore platforms.
- Automotive: Applied in turbocharger rotors and high-performance engine parts.
- Marine: Employed in naval and marine engineering for its resistance to saltwater corrosion.
A Closer Look at Microstructure
In the AM variant of superalloy 718, the presence of numerous dislocation cells creates a network of hydrogen traps. These cells enable faster and more extensive hydrogen absorption, weakening the metal at these sites and causing cracks to form and propagate. In contrast, the wrought Inconel 718 tends to crack along grain boundaries, as it has fewer dislocation cells and more uniform grain structures.
This nuanced understanding of microstructures offers a new perspective on how 718 can be optimized for hydrogen-rich environments. By tailoring the microstructure, particularly in AM alloys, manufacturers can enhance the material’s resistance to hydrogen embrittlement.
Impact on the Hydrogen Fuel Industry
The implications of this discovery are profound for the hydrogen fuel industry, which relies on robust materials to safely store and transport hydrogen. Improved understanding of hydrogen embrittlement in Inconel 718 could lead to the development of more resilient storage tanks, pipelines, and other components critical to hydrogen fuel systems.
With tailored microstructures, 718 can be engineered to minimize hydrogen trapping, thereby extending the lifespan and reliability of hydrogen infrastructure. This not only enhances safety but also reduces maintenance costs, making hydrogen a more economically viable energy source.
To make the superalloy work effectively for hydrogen applications, particularly in the context of hydrogen embrittlement, several strategies can be employed:
- Microstructure Optimization: Tailoring the microstructure of Inconel 718, especially in its additively manufactured (AM) form, is crucial. This involves reducing the number of dislocation cells that act as hydrogen traps. By controlling the manufacturing process, such as adjusting cooling rates and heat treatments, manufacturers can create a more uniform grain structure that minimizes hydrogen absorption.
- Alloy Composition Adjustments: Modifying the alloy’s composition to include elements that reduce hydrogen solubility or enhance the formation of protective surface layers can help mitigate embrittlement. This might involve adding small amounts of elements like titanium or aluminum, which can form stable compounds that block hydrogen ingress.
- Surface Treatments: Applying coatings or surface treatments that act as barriers to hydrogen penetration can protect the underlying alloy. Techniques such as nitriding, carburizing, or applying ceramic coatings can be effective in reducing hydrogen exposure.
- Process Innovations: Developing new additive manufacturing techniques that produce fewer dislocation cells or enhance the uniformity of the microstructure can improve the alloy’s resistance to hydrogen embrittlement. This might include advanced laser or electron beam melting processes that allow for precise control over the microstructure.
- Testing and Simulation: Conducting extensive testing and using simulation tools to predict how Inconel 718 will behave in hydrogen-rich environments can guide the development of more resilient materials. This involves understanding the specific conditions under which hydrogen embrittlement occurs and designing materials to withstand those conditions.
By implementing these strategies, 718 can be optimized for use in hydrogen fuel systems, enhancing its durability and reliability in such applications. This not only supports the safe storage and transport of hydrogen but also contributes to the broader adoption of hydrogen as a sustainable energy source.
Exploring Inconel 718: Can Its Saltwater Resilience Unlock Hydrogen Fuel Production?
The superalloy resistance to saltwater corrosion makes it a strong candidate for applications in marine environments, but using it to address the challenges of producing hydrogen fuel from saltwater involves a different set of considerations.
Producing hydrogen from saltwater typically involves electrolysis, where water is split into hydrogen and oxygen. The presence of salt (sodium chloride) can lead to the formation of chlorine gas and other corrosive byproducts, which can damage equipment. While Inconel 718 is resistant to saltwater corrosion, the process of electrolysis in saltwater introduces additional challenges, such as:
- Chlorine Gas Production: During electrolysis, chlorine gas can be produced, which is highly corrosive and can damage materials not specifically designed to handle it.
- Electrode Material: The electrodes used in electrolysis need to be highly conductive and resistant to both corrosion and the specific chemical reactions occurring during the process.
- Hydrogen Embrittlement: As noted, Inconel 718 is susceptible to hydrogen embrittlement, which could be exacerbated in environments where hydrogen is being actively produced.
While 718’s properties make it suitable for certain components in a system designed to produce hydrogen from saltwater, it may not be the complete solution. The alloy could potentially be used in parts of the system where its corrosion resistance is beneficial, but other materials or coatings might be needed to handle the specific challenges of electrolysis in saltwater, such as chlorine resistance and minimizing hydrogen embrittlement.
Overall, while the AM superalloy can contribute to the durability and longevity of systems involved in hydrogen production from saltwater, a comprehensive approach involving multiple materials and technologies would likely be necessary to fully address the challenges involved.
Conclusion: A Step Towards a Sustainable Future
Inconel 718, with its remarkable properties, stands at the forefront of materials used in extreme environments. The recent insights into hydrogen embrittlement mark a significant step forward in optimizing this alloy for the hydrogen fuel industry. By leveraging scientific discoveries to enhance material resilience, we move closer to a future where hydrogen plays a central role in sustainable energy solutions.
*Additive Manufacturing (AM), commonly known as 3D printing, is a process of creating three-dimensional objects by adding material layer by layer based on digital models. Unlike traditional manufacturing, which often involves subtracting material through cutting or drilling, AM builds up parts from the ground up, allowing for complex geometries and reduced material waste. This innovative approach enables customization and rapid prototyping across various industries.