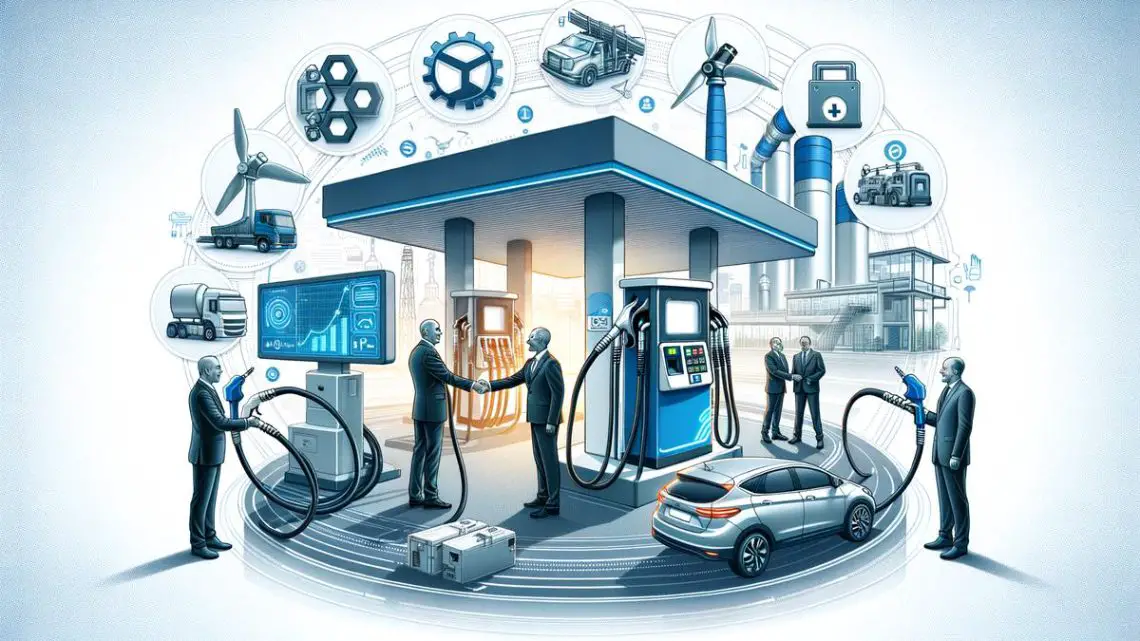
Overcoming the Hidden Challenges of Hydrogen Refueling Stations
August 18, 2024Range anxiety is a genuine concern for hydrogen car owners, manifesting in the tendency of FCEV drivers to refuel when their tanks are just 30% full. This behavior mirrors the initial struggles of electric vehicle (EV) owners, who only overcame their apprehensions through the widespread availability of charging stations.
Similarly, hydrogen vehicles face the need for a comprehensive refueling infrastructure. However, beyond the question of infrastructure lies the challenge of station downtime, whether due to supply shortages or mechanical issues. Fortunately, these hurdles may be less daunting than they appear, offering hope for a smoother path to widespread hydrogen car adoption.
Lets take a look what sorts of issues hydrogen refueling stations are having, what companies make these parts and how we’re going to get past these hurdles.
Hydrogen Fuel Nozzle Freezing
Hydrogen nozzles often freeze due to hydrogen’s unique properties. During refueling, hydrogen gas is highly compressed and cooled to around -423°F (-253°C). This extreme cold causes moisture in the surrounding air to freeze instantly upon contact with the nozzle, potentially causing it to adhere to the vehicle’s fueling port.
An example from California illustrates this issue. Mirai owners encountered cases where the hydrogen nozzle froze to their vehicle, resulting in long waits for technicians to unfreeze the connection. These incidents turned the expected quick refuel into a significant inconvenience for drivers.
At such low temperatures, even minor moisture can cause ice formation. True Zero experienced this when the nozzle would create a seal around itself, immobilizing the vehicle. This necessitated either:
- Waiting for the nozzle to warm sufficiently to detach safely
- Waiting for technicians to apply solutions to unfreeze it
Ambient temperatures further complicate things. In Alberta, Canada, temperatures dropping below -20°C (-4°F) hinder the gas transfer modules, making operations temperamental. Cold weather interferes with the purity of hydrogen fuel, causing condensation that can freeze in the fuel lines.
Various companies like Air Products and True Zero have worked on these nozzle designs. True Zero introduced a new nozzle designed to minimize freezing incidents, demonstrating a practical approach to mitigating this ongoing problem.
The broader issue of hydrogen stations frequently experiencing problems stems largely from the nascent stage of hydrogen infrastructure development. A lack of comprehensive supply chains means stations often run out of hydrogen or suffer mechanical failures.
The solution to these problems involves improved technology and better infrastructure planning. True Zero’s effort to triple station capacities and roll out new nozzles that resist freezing is a step in the right direction. Additionally, ensuring every new station has a backup hydrogen source can mitigate supply disruptions, offering more reliability to hydrogen vehicle owners.
Hydrogen Fueling Station Issues
Hydrogen fueling stations face a range of challenges beyond nozzle freezing, including maintenance issues, supply chain disruptions, mechanical failures, and inadequate infrastructure.
Maintenance issues frequently render stations offline for extended periods. On average, their dispenser systems fail after fewer than 500 uses, which typically results in a malfunction about every 15 days. In contrast, gasoline stations require corrective maintenance roughly every 21.5 days. This means hydrogen stations are less reliable and need repairs more frequently than traditional gasoline stations.
Supply chain disruptions occur due to various factors, including the withdrawal of major players from the hydrogen market. Shell’s exit resulted in the closure of critical hydrogen stations, leaving significant infrastructure gaps. Operators frequently experience outages because of delayed hydrogen deliveries or complications at production facilities.
Mechanical failures contribute to downtime and customer dissatisfaction. Critical components such as compressors and gas transfer modules can fail under constant use or extreme temperatures. True Zero’s experience illustrates this, where compressors sometimes require reboots between fills, adding time to the refueling process.
How to Refuel a Hydrogen Car:
Infrastructure Challenges:
- Only 52 hydrogen refueling stations nationwide in the United States
- Inadequate network to meet growing consumption demands
- Longer travel times to reach operational stations
- New stations take up to 18 months to construct
- Each station costs well over a million dollars
Addressing these problems requires substantial investment in infrastructure, technological innovations to handle extreme conditions, and stronger supply chain partnerships to ensure reliability.
Hydrogen Nozzle Development
Several companies are at the forefront of advancing hydrogen nozzle technology:
Air Products: A leading supplier of atmospheric gases and services, focuses on improving nozzle durability and reliability. Their operational staff provide firsthand insight into the practical challenges faced by hydrogen drivers.
True Zero: Has introduced a new nozzle design aimed at reducing freezing incidents. Their advanced nozzle incorporates high-performance polymers and alloys, which resist extreme cold better than traditional materials, enhancing structural integrity and lifespan.
Iwatani Corporation: Contributes to hydrogen nozzle technology by leveraging advanced materials and engineering to design nozzles that operate efficiently under adverse conditions. Their collaborative efforts have helped propagate improved nozzle designs across multiple refueling stations, particularly in California.
Collaboration between these companies and auto manufacturers like Toyota has been crucial in refining the usability and reliability of hydrogen nozzles. These partnerships ensure compatibility and reliability across different refueling stations and align refueling standards with the operational needs of hydrogen vehicles.
As these companies continue to refine their designs and expand infrastructure, the viability of hydrogen as a sustainable fuel source improves.
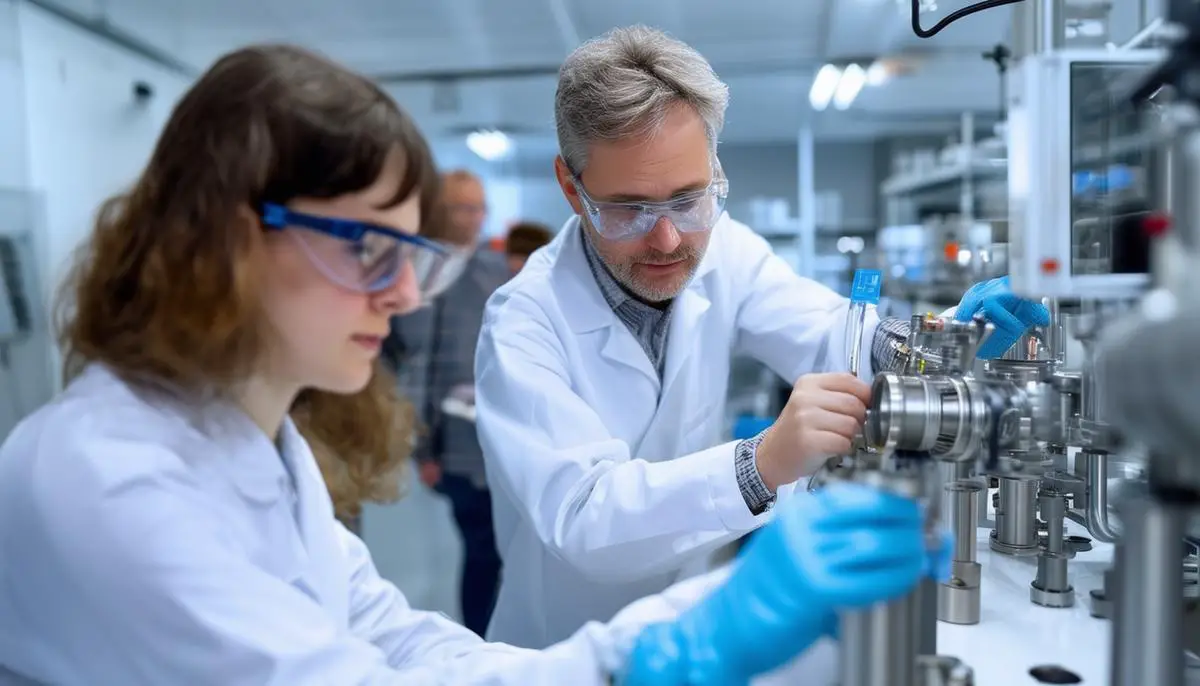
How a Hydrogen Refueling Station Works
A hydrogen refueling station is a facility designed to fill hydrogen-powered vehicles with compressed hydrogen gas. The basic operation involves several key components and processes to ensure efficient and safe refueling.
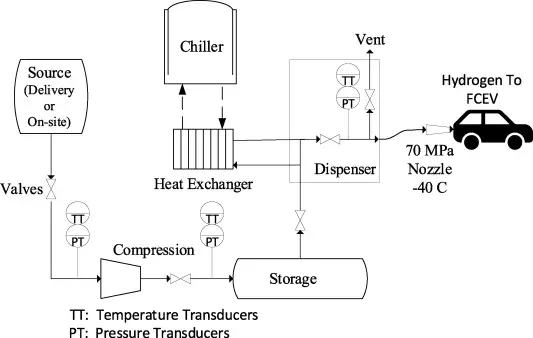
Image Credit ScienceDirect
Key Components:
-
Compressor: The hydrogen gas, whether produced on-site or delivered from an off-site source, is compressed to the required pressure using a compressor.
-
Storage Tank: Once compressed, the hydrogen is stored in a pressurized tank until it is needed for vehicle refueling.
-
Pre-cooler: Before filling a vehicle, hydrogen is cooled to -40°C by a pre-cooler. This cooling process is essential to prevent overheating during the transfer of hydrogen into the vehicle’s tank.
Types of Stations:
- On-site Stations: Produce hydrogen directly at the station using resources like city gas and water.
- Off-site Stations: Receive hydrogen transported from an external production site.
- Fixed Stations: Operate at permanent locations similar to traditional gas stations.
- Mobile Stations: Mounted on trailers, they can be moved to different locations as needed.
- Integrated Stations: Combine traditional fuel services with hydrogen refueling capabilities.
Process Overview:
- Hydrogen Production/Transportation: Depending on the station type, hydrogen is either produced on-site or transported from another location.
- Compression and Storage: The hydrogen is compressed and stored until it’s needed.
- Cooling and Dispensing: The pre-cooled hydrogen is then dispensed into the vehicle’s tank.
Measurements Taken:
To ensure safety and efficiency, several measurements are consistently monitored at hydrogen stations:
- Gas pressure and temperature are measured at various points, including before and after compression and during dispensing.
- The storage system’s state of charge and cycle counts are tracked.
- Vehicle tank temperature, pressure, and volume are recorded during refueling.
These stations are equipped with sensors and controls to manage the flow, pressure, and temperature of hydrogen, ensuring a safe and efficient refueling experience for hydrogen-powered vehicles.
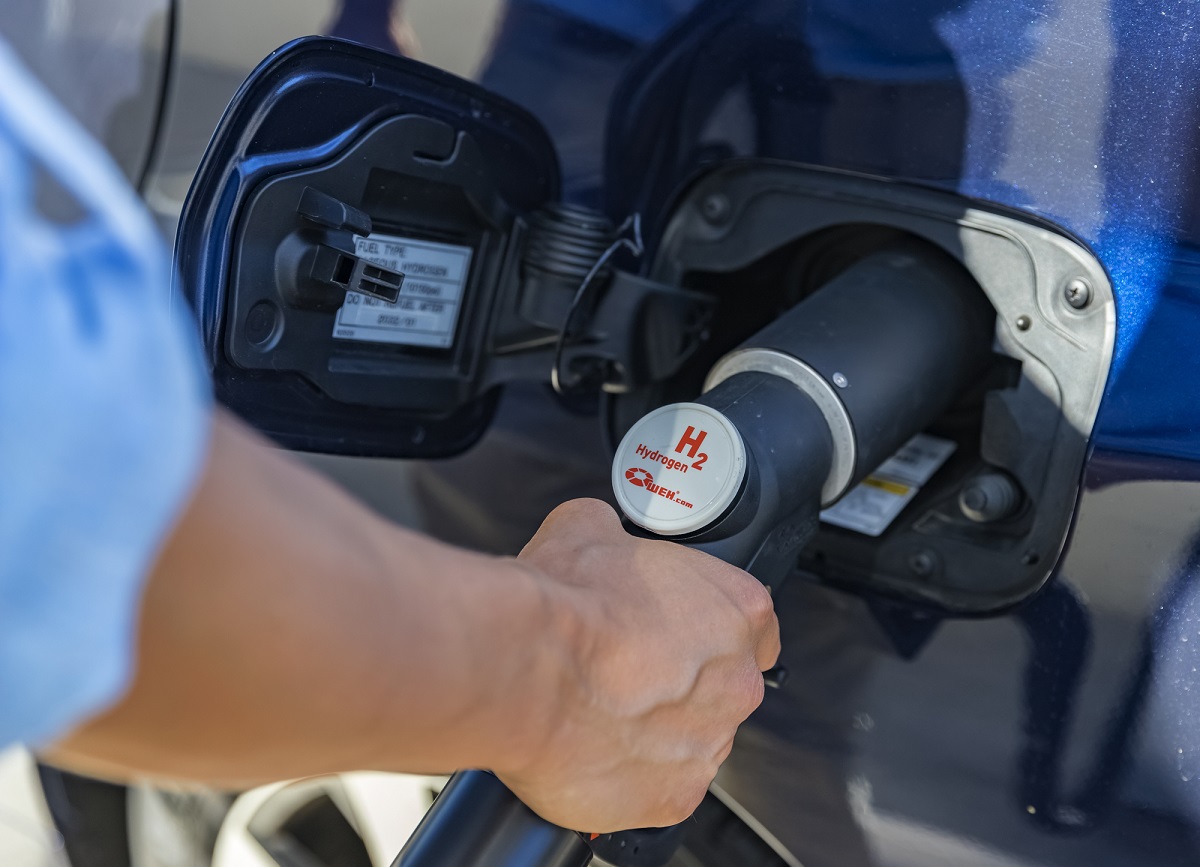
Credit: Photo by depositphotos.com
Improving Reliability and Solutions to Hydrogen Fueling Problems
Addressing hydrogen fueling challenges requires a multi-faceted approach:
- Material Innovation: Continued research into more robust and temperature-resistant materials for nozzles and other components.
- Mechanical Reliability: Adoption of advanced compressor technologies with higher operational thresholds and improved maintenance routines.
- Infrastructure Enhancement: Incorporating redundancy into the fueling network and prioritizing rapid deployment of additional stations.
- Regulatory Support: Government policies promoting hydrogen technology development, coupled with financial incentives to accelerate the deployment of advanced refueling stations.
- Industry Collaboration: Shared knowledge and co-development initiatives among major players to tackle specific challenges.
- Best Practices Adoption: Scaling proven models to other regions and incorporating insights from successful international hydrogen networks.
- Long-term Strategies: Investing in smart grid technologies to optimize hydrogen production based on renewable energy availability and embracing digital solutions for predictive maintenance and real-time monitoring of station performance.
The advancement of hydrogen refueling stations is an evolving area, yet one promising approach to optimize their efficiency is the implementation of the PHM (Prognostics and Health Management) model. According to a study, adopting a unified set of maintenance guidelines across all existing stations can significantly minimize downtime for drivers. The key to this strategy is proactive maintenance, which involves initiating each day with thorough equipment check-ups.
As these stations require more technicians trained specifically in hydrogen refueling equipment maintenance, such specialized training is crucial to effectively execute the PHM model and proactive strategies. By addressing potential issues before they escalate, this approach is estimated to reduce costs by up to 30% compared to unscheduled maintenance, as evidenced by findings from other industries.
In conclusion, the adoption of standardized maintenance practices and proactive strategies in hydrogen refueling stations offers substantial benefits in reducing both downtime and operational costs. By drawing on successful preventative maintenance models from other industries, the hydrogen sector can enhance reliability and ensure a smoother refueling experience for drivers, ultimately supporting the wider adoption of hydrogen as a sustainable energy source.