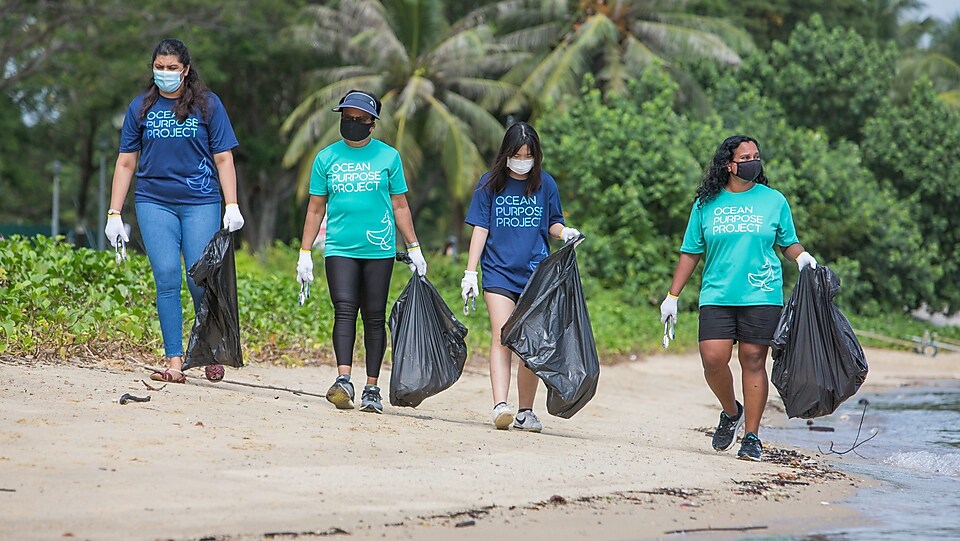
Ocean Purpose Project plastic to energy project is moving forward at full power
August 20, 2021 0 By Julie CampbellUnder Shell’s mentorship, this start-up converts ocean plastics into usable H2.
Ocean Purpose Project has announced that they are moving ahead full tilt with a plastic to energy project developed to cut global plastic pollution levels at scale.
The program collects waste plastics for conversion into high profit products that funds their purpose- helping polluted coastal communities.
The Ocean Purpose Project is calling this strategy a world’s first. This plastic to energy (PTE) solution will convert waste plastics (among them non-recyclable ocean plastics) into hydrogen gas, carbon nanotubes (CNT) and low sulphur oil. The goal is to pivot from mechanical recycling to chemical recycling with a circular solution for ocean plastics that Ocean Purpose Project collects in beach clean ups at their homebase of Pasir Ris, Singapore that would otherwise have been ocean bound.
Ocean Purpose Project’s solution was selected as one of the top 5 start-ups mentored by the Shell Startup Engine and the Energy Market Authority of Singapore. Their in-house engineering team of researchers and ex-Alstom engineers are collaborating with a diverse spectrum of partners from Germany, Singapore and India. Currently their efforts have been focused on developing a prototype proposal for a working PTE Unit called the OPP PTF Unit with commercial viability within two years.
Their plastic to energy method is undergoing extensive development to ensure safety and practicality.
Ocean Purpose Project was founded in 2020 by Singaporean Mathilda D’Silva, now the company’s CEO. Mathilda, a victim of water pollution herself felt compelled to solve the ocean pollution crisis through small scale ocean projects. In 2019, she partnered with her friend Lisa Jones, a Pilates teacher in Indonesia to work on a highly simplistic PTF (Plastic to Fuel) machine that converts 300 kilograms of waste plastics into 3 liters of fuel per day. This original process used pyrolysis to convert the waste material into the usable fuel.
In Indonesia, the project achieved success among Medang’s islanders because it turned plastic pollution into what was essentially free low sulphur fuel. That said, it was clear that this method required substantial development in order to scale it up to make it worthwhile. Unfortunately, the original budget of SGD 10,000 (approximately USD7,300) deemed it impossible to ensure that best in class technology would be employed with health and safety standards would be met.
As a result, Ocean Purpose Project developed its own world-class PTE unit that fit inside a 40ft container created in conjunction with industry and petrochemical leaders to be certain that it would minimize all safety, health, and environmental risks.
The current plastic to energy unit transforms waste plastics into condensable and non-condensable hydrocarbon gases using pyrolysis. The unit is then able to generate low sulphur fuels, carbon nanotubes (CNT) and hydrogen fuel. The unit’s carbon nanotubes (CNT) output is about 100 kilograms per metric ton of plastics. The hydrogen output is in the range of 14 to 17 kilograms.
When taking the 80 percent conversion efficiency level into account, it will mean that 1 metric ton of plastics can potentially be converted into about 11 to 14 kilograms of hydrogen fuel. Uses abound as the 40ft unit can travel over land and sea to be parked next to polluted beaches or landfills, churning plastic waste into highly profitable circular products. Ocean Purpose Project is eager to mobilize more avenues of ocean plastics through encouraging partnerships between NGOs and governments and is looking to work with more institutions of higher learning to improve it’s hydrogen production to impact regions beyond Singapore that are plagued by plastic pollution.
About The Author
Julie Campbell is a veteran news writer with a primary focus on hydrogen fuel and renewable energy, technology, health and wellness. Campbell has been the head of a freelance writing company since 2003...READ MORE