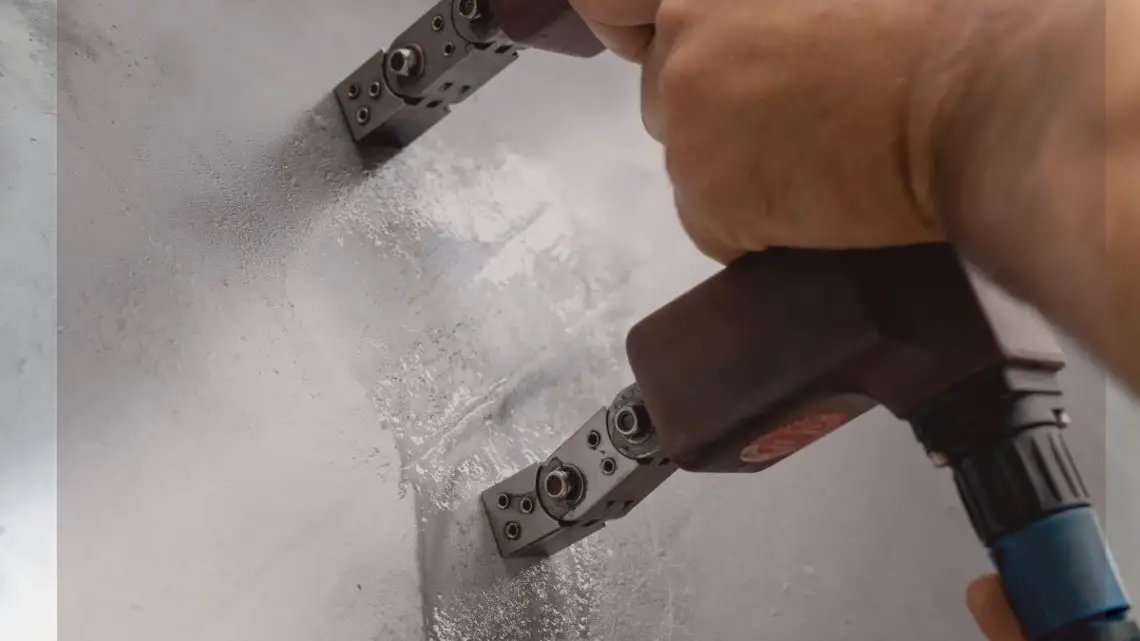
How to Repair a Defective Weld through X-Ray?
November 5, 2021 0 By Sponsored ArticleIntroduction
Do you often find it challenging trying to repair defective welding jobs?
The truth is that many anomalies can plague a welding job but knowing the cause of the defects should be the first step to repairing these irregularities.
Notwithstanding, a tool that can accurately help you identify these defects is also essential, and one outstanding piece of equipment is the welding X-ray machine.
This machine comes with many benefits that make it the most suitable tool for identifying and analyzing welding defects.
However, you need to know the common types of welding errors that you might encounter to prepare for them adequately.
I. What is X-ray Inspection in Welding?
Welding is important in the manufacturing industry. However, many defects occur during this process that reduces the integrity of welding and the quality of final products.
The ability to identify these anomalies during welding is critical to finding a lasting solution to the problem of substandard product manufacturing.
X-ray inspection is a non-destructive testing technique that offers tremendous benefits in identifying errors during welding using X-ray energy.
It is also a very accurate inspection method as it can penetrate hidden features that are difficult for other quality assessment methods like visual inspections.
II. How are X Rays Used to Detect Faults in Welds?
X-ray welding inspection helps to assess the quality of welding using X-ray radiations. The machine projects radiation on the welded sample, and the sample absorbs some of the radiation, with the remaining radiation going to the detector.
The detector can generate an image based on the amount of radiation it receives. The analysis of this image helps the trained inspector analyze and identify the anomalies present in the weld.
X-ray machines enable the inspector to zoom into the image to see tiny features in detail, which helps to identify hidden and difficult-to-spot errors.
However, the image quality, which is determined by the x-ray tube’s capacity, is critical for the accurate assessment of the weld. This reason is why it is often advisable to purchase X-ray machines with high definition and magnification from a reputable X-ray machine manufacturer like Uni X-ray.
III. What are Common Types of Weld Defects?
Various defects plague welding jobs, and these deficiencies can reduce the quality of the final product.
Additionally, a change in physical features of the product, including size, shape, and dimensions, can occur because of the flaws.
Some of these deficiencies are the result of using wrong welding procedures or substandard welding material.
However, recognizing the various welding anomalies that you may encounter when carrying out welding jobs will let you know how to avoid them.
Here are some of the most frequent welding errors you may encounter with their causes and solutions.
- Cracks
- Description
A crack is a form of discontinuity often found on the surface of a welded joint. However, there are cases where cracks are hidden beneath a layer of welded joints making it difficult to detect.
Sometimes, the intense heat used during the welding process can cause a crack around the region.
Nonetheless, the three types of cracks include hot cracks, which occur while the welding is ongoing, cold cracks arise after completion, and crater cracks after welding has solidified.
- Causes
Here are the typical causes of the different types of cracks described above.
- The metal contains Carbon and Sulphur in high proportions
- Welding ferrous metals using hydrogen
- Neglecting the preheating process before welding
- Contamination of the base metals used in welding
- Inadequate joint design
- Stresses that result from the shrinkage of the weld joint during solidification
- Using low welding current while welding at very high speeds
How to Repair
There are various ways to repair cracks, and some of them are listed below, including:
- Using suitable current for the welding speed
- Rid the base metal of impurities
- Ensure the metal undergoes adequate preheating
- Use the right metal
- Ensure you fill the crater adequately to avoid crater cracks
- Ensure the joint design is adequate
- Ensure you cover sufficient area of the weld joint
- Make sure to cool the welded area appropriately
Porosity
- Description
When voids filled with air bubbles occur in welded joints due to impurities on the surface of the metal, this is known as porosity. This defect often causes a weak point in the weld which can fail the final product.
- Causes
Here are the typical causes of porosity
- Existence of oil or grease and dirt on the metal surface
- Longer arc usage
- Inadequate gas shield
- Presence of impurities on the surface
- Existence of water or moisture on the surface
- Improper deoxidation of electrode
- Inadequate surface cleaning
- Gas flow is too high
How to Repair
To repair porosity in a weld, you can take the following steps
- Make adequate pre-welding surface preparation
- Ensure the use of a suitable welding procedure
- Ensure adequate arc distance
- Set the gas flow with a sufficient flow pressure
- Employ the correct electrode
- Make sure materials and the electrodes are dry
- Ensure the gas travel speed is adequate to eliminate trapped gas
Slag Inclusion
- Description
When the protective flux material melts during the welding process, it can include the waste slag material in the weld.
- Causes
The causes of slag inclusion can include
- Uncleaned weld pass at the beginning of welding
- Wrong weld angle
- Low welding current
- Excessive welding speed
- Inadequate surface cleaning
- Excessive cooling speed
How to Repair
Follow the following steps to repair slag inclusion error
- Use correct welding angle
- Ensure the surface is adequately cleaned
- Clean the weld pass at the beginning of the welding
- Use appropriate welding speed
- Clean off any slag from the preceding bead
Incomplete Fusion
- Description
Incomplete fusion is the resulting discontinuity from the lack of proper bonding of the weld metal and base metal. It is often seen when the molten metal does not fill the gap between the weld joints.
- Causes
Here are some reasons for the presence of incomplete fusion during welding
- Inadequate welding heat
- Impurities formed on the welding surface
- Wrong electrode angle
- inappropriate choice of electrode size for welded metal thickness
- excessive welding speed
- excessive weld pool
How to Repair
Take the following steps to avoid encountering incomplete fusion during welding jobs.
- Ensure the use of adequate welding current
- Ensure the metal is clean before commencing the welding
- Ensure the weld pool is not excessive
- Employ the right electrode type and size
- Ensure you use adequate electrode angle
- Ensure the right amount of deposit per time
Overlap
- Description
Overlap occurs because of an overflow of the weld pool over the welding surface, preventing the fusion of the molten metals with the weld metal.
- Causes
- Excessive deposits of weld per time
- Using the wrong welding technique
- Incorrect electrode coating
- Inadequate welding angle
- Excessive welding heat
How to Repair
To repair overlapping in welding, here are some steps you can take
- Employ the proper welding technique
- Use the correct welding angle
- Position the weld materials on a flat plane
- Ensure the correct weld deposition per time
- Avoid excessive current that may cause overheating.
Undercuts
- Description
When uneven welding hollows occur on the weld metal during welding, it is known as an undercut. This error is often seen to have cavities with certain sharpness, depth, and length.
- Causes
Here are some of the reasons for undercuts during welding
- Employing an incorrect filler metal
- Using excessive welding current
- Applying excessive welding speed
- Inappropriate protective gas choice
- Inaccurate welding angle
- Selecting the wrong electrode type and size
How to Repair
To avoid undercuts during welding, you can follow the steps below
- Use the appropriate filler metal
- Employ the right welding current
- Reduce the welding speed
- Select the right protective gas
- Use adequate welding angle
- Choose the right electrode type and size
Spatter
- Description
Spatter often occurs with gas metal arc welding, and it is the result of the bonding of tiny particles to the areas around the welding spot.
- Causes
Many things can lead to the occurrence of spatter in welding, including
- Incorrect welding current
- Low voltage settings
- Wrong polarity
- Impurities on the metal surface
- Inappropriate welding angle
- Inconsistent wire feeding
How to Repair
Take the following steps to avoid this error during welding jobs
- Ensure the welding surface is clean before the commencement of welding
- Check the polarity to ensure it is correct
- Ensure adequate voltage settings
- Choose the suitable welding current
- Ensure you use an acceptable welding angle
- Correct any feeding issues
Conclusion
To wrap up, you need to be aware of common welding errors that might come up during your welding jobs. But it would help if you also had accurate means of assessing the quality of the weld and spotting any anomalies during the welding.
X-ray welding inspection offers several benefits that make it very suitable for assessing welding quality, including accurate error identification and fast result generation.
Nonetheless, you should ensure that your X-ray machine has a good X-ray tube and purchase from a dependable X-ray machine manufacturer.
One such manufacturer is Uni X-ray, with almost two decades of consistent quality delivery.